Chemical phosphoric acid activated carbon production process
The phosphoric acid method for producing activated carbon is a commonly used chemical activation process. It mainly uses phosphoric acid as an activator to convert carbon-containing raw materials (such as wood, coconut shells, fruit shells, etc.) into activated carbon with a high porosity structure at high temperature. The following is a brief introduction to the method:
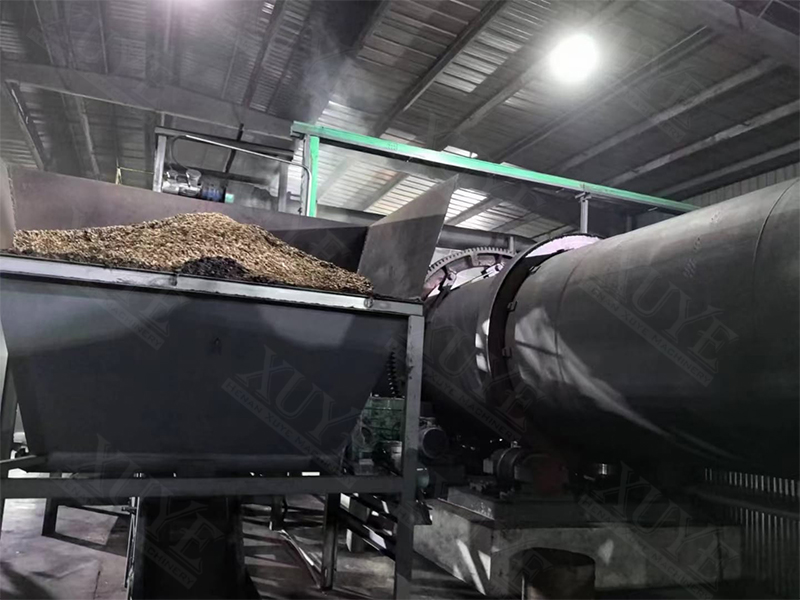
- Basic principle
Phosphoric acid plays the following roles during the heating process:
Dehydrating agent: promotes the removal of moisture and volatiles in the raw materials, inhibits tar formation, and reduces carbon loss.
Oxidant: reacts with cellulose and lignin in the raw materials to form a cross-linked structure and expand the pores.
Template effect: phosphoric acid penetrates into the raw materials, leaving abundant pores (mainly mesopores) after pyrolysis.
- Production process
Raw material pretreatment
The raw materials are crushed to a suitable particle size (usually 3-10mm) and impurities are removed.
Impregnation
Mix the raw materials with phosphoric acid solution in a certain proportion and soak for several hours until uniform penetration.
Activation
In an inert atmosphere (such as nitrogen) or oxygen-limited conditions, heat to 400-600℃ for 1-2 hours to allow phosphoric acid to fully react with the raw materials.
Recover phosphoric acid
After activation, wash with water until neutral and recover phosphoric acid (recyclable).
Drying and crushing
The washed activated carbon is dried, crushed, and sieved to obtain the finished product.
- Product features
Developed pores: mainly mesopores, suitable for adsorbing larger molecules (such as pigments, organic matter).
High specific surface area: usually up to 1000-1500 m²/g.
Surface oxygen-containing functional groups: phosphoric acid activation will introduce acidic groups and enhance the adsorption of polar substances.
- Advantages and disadvantages
Advantages:
Low activation temperature (compared to physical methods) and low energy consumption.
Controllable pore structure and excellent adsorption performance.
Disadvantages:
Waste acid needs to be treated, and the environmental protection cost is high.
The equipment needs to be resistant to acid corrosion (such as enamel or stainless steel).
- Application areas
Water treatment: removal of heavy metals and organic pollutants.
Food industry: decolorization, refined sugar solution.
Chemical industry: catalyst carrier, gas purification.
- Environmental protection and improvement
Phosphoric acid recovery: reduce waste liquid discharge through evaporation concentration or neutralization treatment.
Green alternative: study the activation process of biomass acid (such as citric acid) or low-concentration phosphoric acid.
The phosphoric acid method occupies an important position in the industry due to its high efficiency and controllability, but it needs to balance performance and environmental protection requirements.
التوصيات ذات الصلة
-
عملاء كنديون زاروا مصنع شويي للماكينات
418Xuye Machinery provides Canadian customers with a complete set of solutions for activated carbon production lines, covering crushing, activation, and recovery systems, supporting customized needs and compliance with environmental standards.
عرض التفاصيل -
شركة فرنسية زارت خط إنتاج الكربون المنشط لشركة Xuye وأشادت بالابتكار التكنولوجي ومعايير مراقبة الجودة
333How can activated carbon production lines achieve efficient and large-scale production? It covers physical and chemical (phosphoric acid/zinc chloride) processes, and provides equipment selection, environmental protection solutions and industry ap...
عرض التفاصيل -
أكملت شركة Xuye Machinery بنجاح تركيب خط إنتاج معدات الكربون المنشط
376The core equipment of the activated carbon production line (carbonization furnace, activation furnace, etc.), process flow (physical method/chemical method), investment cost and environmental protection requirements are suitable for industrial pro...
عرض التفاصيل -
فيديو خط إنتاج الكربون المنشط للعملية الكيميائية
316Analyze its activation principle, production process, specific surface area advantages, and its applications in environmental protection, food and other industries.
عرض التفاصيل